Overview
Single beam truck is commonly used equipment in industrial field, which is used to realize the movement of goods in three-dimensional space. Among them, the operation of the two directions of the horizontal plane is completed by the large, the car, the vertical direction of the operation is responsible for the lifting of the electric hoist mechanism, the electric hoist is a two-speed conical motor, the electric control mode is basically the AC contactor direct start, the impact current is too large, easy to cause damage to the motor and components, mechanical equipment life is shortened, the maintenance amount is relatively large. And the speed regulation characteristic is poor, debugging is not smooth enough.
The characteristics of electric hoist operation
The crane has a large starting torque, usually more than 150% of the rated torque, if considering overload and other factors, at least 200% of the rated torque should be provided during the starting acceleration process.
Whenthelifting mechanism is running down, the motor will be in a regenerative po-wer generation state and it must be subjected to energy consumption braking or reg-enerative feedback to the grid.
The load of the lifting mechanism changes sharply when the lifting weight leaves or touches the ground, and the inverter should be able to smoothly control the impact load.
KD600 inverter features
- Magnetic field oriented current open loop vector control, motor variables are comple-tely decoupled, with low frequency torque, fast response speed and other character-istics;
- KD600adopts PG-free open loop vector control mode and vectorized V/F mode to enlarge the power level of one step;
- Frequency range: 0.5-600Hz stage setting, stepless continuous adjustment;
- Workingvoltage range: 380V±20%, bus voltage instantaneously as low as 360VDC trouble-free operation;
- Overloadcapacity: 150% rated current, allow 1 minute; 200% rated current, 1 second allowed;
- Torque characteristics: starting torque, more than 2 times the rated torque; Low frequ-ency torque, 1Hz greater than 1.6 times the rated torque; The braking torque is great-er than the rated torque.
Simple wiring diagram
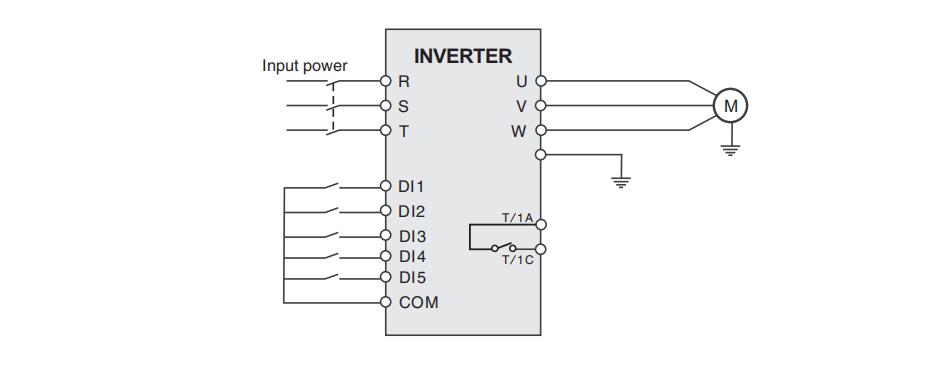
Reference parameter Settings and descriptions are as follows
Function Code | Set Value | Instruction | Remark |
P0-03 | 1 | Vector mode | |
P0-04 | 1 | terminal control | |
P0-06 | 4 | multi-speed frequency | |
P0-23 | 3 | acceleration time | |
P0-25 | 5 | deceleration time | |
P6-00 | 32 | Brake control | |
B5-00 | 1 | Brake enable | |
B5-01 | 2.5 | Release brake frequency | |
B5-04 | 1.5 | Brake frequency | |
P4-01 | motor power | ||
P4-02 | motor voltage | ||
P4-04 | motor rated current | ||
P4-05 | motor rated frequency | ||
P4-06 | motor speed | ||
P5-00 | 1 | Forward | |
P5-01 | 2 | reverse | |
P5-02 | 12 | multi-speed 1 | low speed |
P5-03 | 13 | multi-speed 2 | middle speed |
P5-04 | 14 | multi-speed 3 | high speed |
PC-01 | low speed frequency | ||
PC-02 | middle speed frequency | ||
PC-04 | high speed frequency |
Operation effect analysis
KD series inverter conversion transformation of the driving system, the transformation effect is ideal, mainly in:
- Soft start and soft stop are realized when starting, reducing the impact on the power grid.
- The use of frequency converter to eliminate the original shift contactor and speed resis-tance, that is, to save maintenance costs, but also reduce the downtime maintenance time, thereby improving the output.
- The main hook working at 5Hz~30Hz can have a very obvious effect.
- Improvethe field process, save raw materials;
Closing remarks
The use of a frequency converter to control the front and rear travel, as well as the left and right travel mechanism series, can achieve over frequency operation, greatly improving work efficiency while ensuring safety, and also reducing the maintenance workload of frequent replacement of AC contactors in driving equipment.
Application site
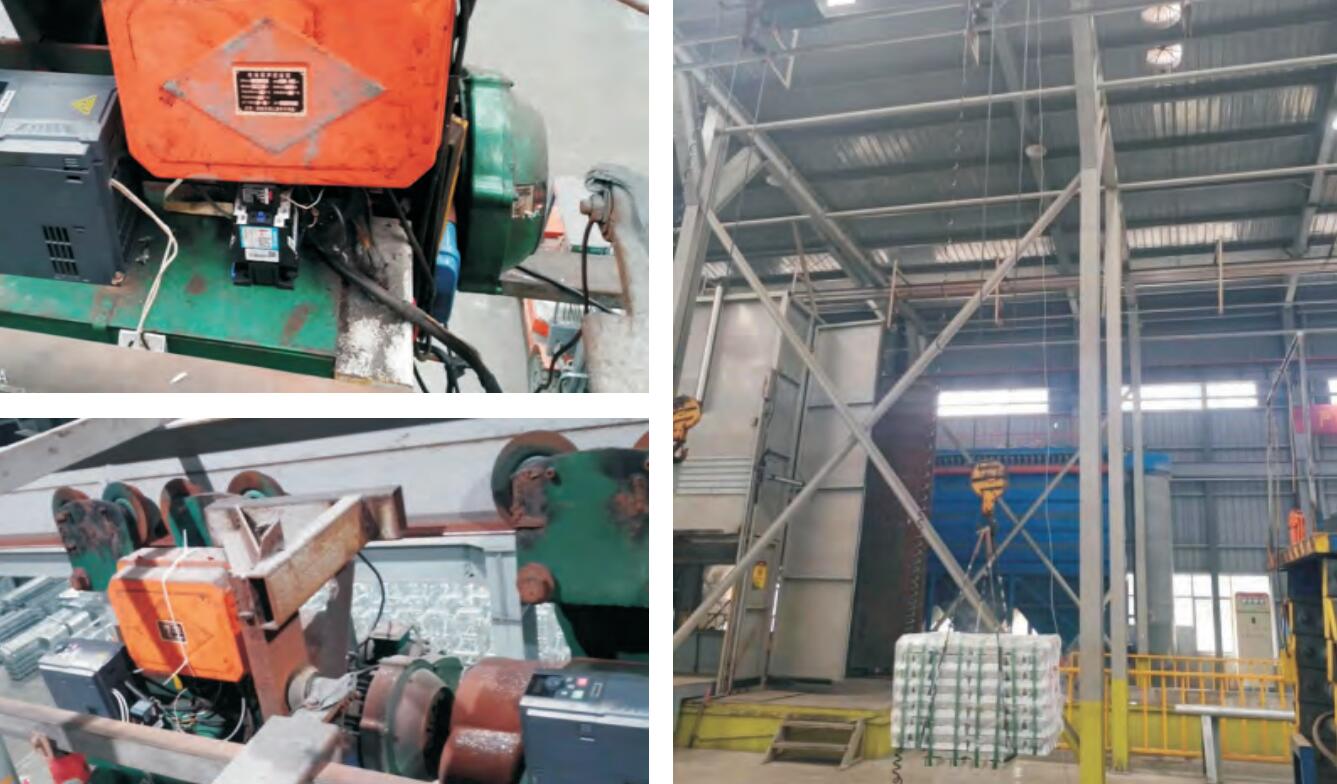
Post time: Nov-17-2023